Jewelry Crafting: Mokume Gane
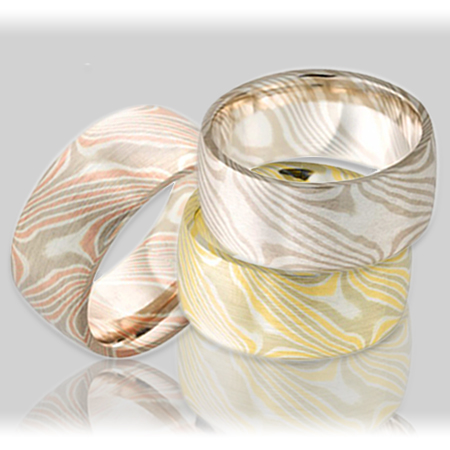
Let’s say you and your love have an important anniversary coming up. Let’s say too that it’s your five-year wedding anniversary. According to traditional anniversary gift guides, five years together is to be celebrated with wood. Wood. But before you go pulling a twig off your backyard tree (which is not going to win you any points, believe me), consider taking the road less traveled. Jewelry is always welcome, and Timeless Wedding Bands has something that fulfills the traditional wood gift with a modern jewelry twist.
Mokume gane is a Japanese metal process that yields stunning pieces of metal work with the look of a natural wood grain. Literally translated, mokume gane means “wood eye metal” or “wood grain metal.” This amazing and highly technical process originated with decorative sheathing and handles for samurai swords in 16th and 17th century Japan.
Over time, as the traditional caste system disintegrated and the demand for ostentatious sword decorations as a status symbol fell, the number of skilled metalsmiths who had mastered mokume gane dwindled. Those who remained in command of the skills necessary to produce this stunning metalwork shifted their skills to producing jewelry and other smaller decorative objects.
Traditionally, softer metals and alloys have been used to create mokume gane. Gold, silver, copper, and shakudō (a Japanese copper alloy containing between 2 and 4 percent gold) were most often used. In the traditional process, a diffusion process is used to fuse the layers of metal together. To begin, the master metalsmiths take sheets of metal, clean them meticulously and grind them down until they are perfectly flat. They then stack them in whatever pattern or arrangement they want. This stack of metal sheets is then heated with the utmost care and attention. In the diffusion process, the metal sheets are heated to just past a solid state, just before they are molten. In this half-melted state, the metals bond together. There is no other chemical process or anything like that. Just heat. This process of fusing the sheets together is called lamination. The use of solder to laminate the sheets has been employed, but the solder flux can easily introduce impurities to the metal sheets, creating unsightly irregularities that need to be cut out. The metals then need to be resoldered, which opens the door for the same types of problems.
The resulting stack of laminated sheets is called a billet. A cross section of the billet looks like a simple striped metal block. To get the eye-catching wood grain look, the billet is cut and carved to reveal different metal layers. Then the billet is flattened. These two steps are repeated until the desired mokume pattern is achieved. This wood grain metal can now be used to manufacture all sorts of decorative objects.
The process for jewelry varies some, with the semi-molten billet being wrapped around a rod of a specific ring diameter. The billet rod then alternates between hand tamping (hammered with a mallet) and heat exposure (to keep the metal malleable) to coax the mokume pattern out of the metal. This handcrafting process is highly technical and requires a very skilled artisan. But the resulting ring is one that has no solder lines or seams. The ring has no beginning or end. It was formed from the beginning as one solid piece.
Traditionally produced mokume gane stayed primarily in the Pacific Rim and through the years, as the remaining artisans were lost, mokume gane nearly went extinct with them. However, in the 1970s, two people, Eugene Michael Pijanowski and Hiroko Sato Pijanowski brought mokume gane to the United States. Once stateside, the artform captured the public’s attention and appreciative eye.
With the rekindling of mokume gane love came some modern process interpretations. Many mokume gane items are now solid-state bonded. This starts with the same basic processes as the traditional ways, but where the traditional way only uses heat, the modern process introduces pressure to assist in the lamination process. By using hydraulic presses to compress and fuse the metal layers, the metal doesn’t need to be heated to as high of a temperature. This lower temperature, higher pressure lamination has allowed for other metals, like titanium, bronze, and platinum, to be added to the billet.
Timeless Wedding Bands is honored to offer rings made with this beautiful metalsmithing skill. Our Mokume Star Wedding Bands are available in different metal color combinations to suit the most discerning spouse. Available in widths ranging from 5 mm to 8mm, the rings will be equally magnificent on the hand of the bride or groom. Treasuring the time-honored traditions of jewelry crafting allows us all to hold onto (literally) the skilled arts. And by mixing up your anniversary gift (remember, nobody wants to unwrap a bundle of branches), you can cherish the traditional with modern sensibility.
Until next time,
Rebecca Judkins
Share This Page: